The Birth of a Elitecustomtable Table
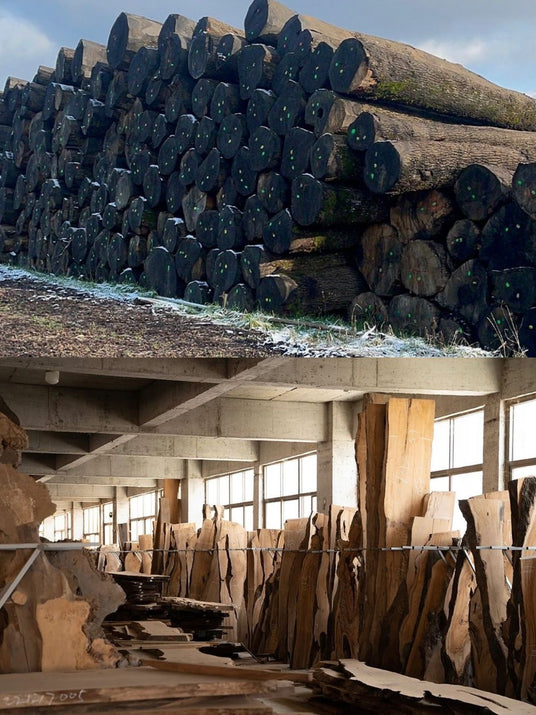
1. Log Selection: Using rare logs for all epoxy resin tables
The creation of an excellent table is inseparable from the selection of a top - notch log. The wood - selection team of Elitecustomtable has scoured the world and formed strategic partnerships with the world's premier timber suppliers. Each log is obtained from sustainable forest farms that are certified by PEFC and chosen from complete and gigantic logs that are over 100 years, with well-preserved bark, little cracking in the heartwood, clear and smooth grains, and possessing characteristic natural shapes.
2. Sawing: A test for skillful carpenters
In order to make full use of the whole log without losing the best grain effect of each material, Elitecustomtable's board - making carpenters, relying on their experience and discernment, consider the overall sawing method. They are committed to ensuring that each rough board maintains a thickness of 7 - 8 cm. By only selecting the 3rd to 5th layers in the center, it is guaranteed that these boards exhibit a clear and beautiful grain with flat beveled edges.
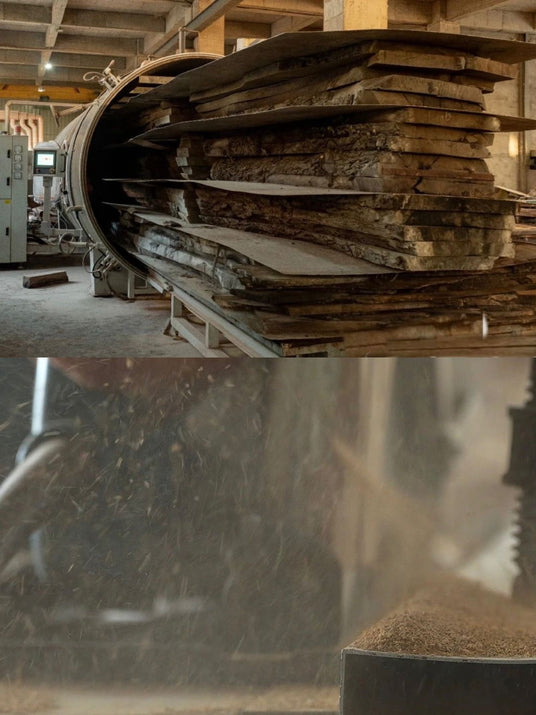
3. Drying: A Key and strict processing procedure
The drying process of wood is the most crucial step in the production of all solid wood furniture. If the solid wood is not dried adequately, it is highly susceptible to cracking, deformation and even insect infestation. After a long - term monitoring of wood's moisture content, the Elitecustomtable team discovered that the wood is most stable when its moisture content is 12°. Thus, we use professional drying machines to keep the moisture content of the wood within this temperature.
4. Cutting: Combining experience and aesthetics
The quality of the cutting process directly determines the quality of a board's product, which requires absolute experience in cutting and excellent aesthetics on the part of the board maker. The master carpenters at Elitecustomtable are able to proficiently cut out the large - board edge shapes with parallel and neat ends, discard the defective parts and retain the most perfect appearance of the original wood.
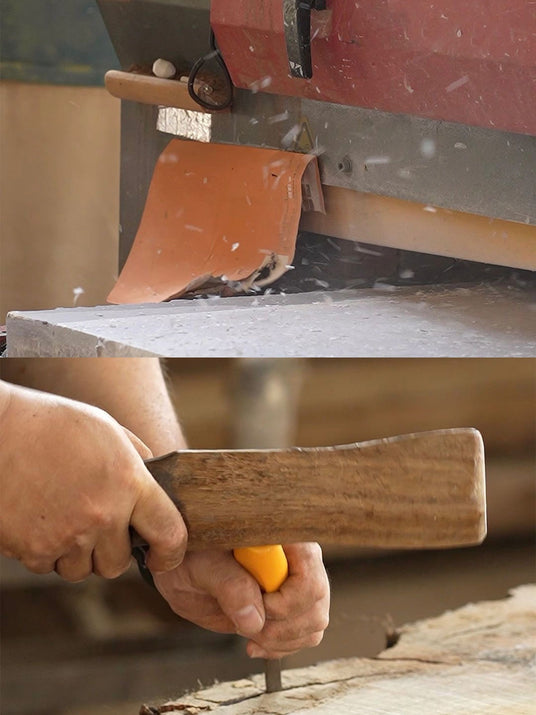
5. Wood Calibration: Employing rigorous high - frequency Machines.
Elitecustomtable introduces high - frequency calibration machines. Through the balanced transfer of heat inside a board and pressing, the warped board is flattened, which not only reduces the moisture difference between the inside and the outside of a board, but also reduces the possibility of warping and cracking phenomenon that may occur in the future in the process of using the board.
6. Sanding: To ensure the thickness of the board
Elitecustomtable uses advanced sanding machines imported from Japan to flatten the boards. A board needs to be peeled back and forth sand 10-20 times to ensure that the surface has no waves or undulations, and that the thickness of the board is the same everywhere. This can avoid the risk of unevenness caused by manual planing and maximize the restoration of the natural texture of the large - board table itself.
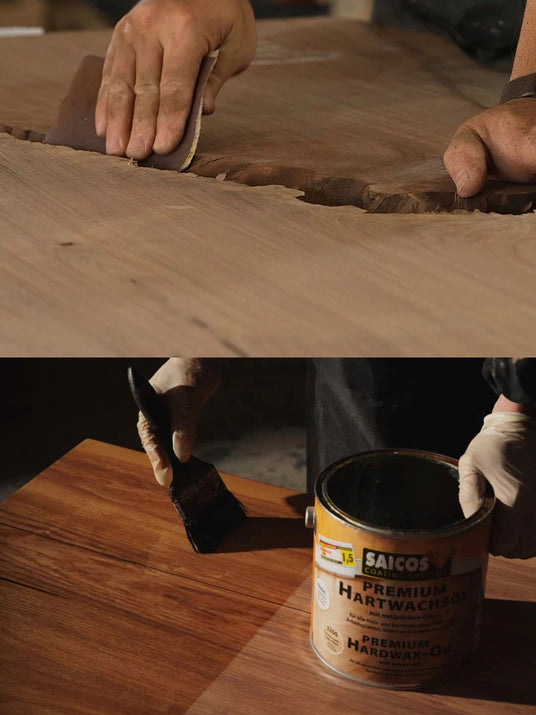
7. Polishing: A purely handmade processing
Elitecustomtable leaves no detail untouched, even the smallest edges of the boards are carved with the utmost care. Relying on our skillful craftsmanship, the outer layer of the wood is removed while the natural part of the original wood's edge is retained. Then, hand - sanding is carried out, starting from 120 - grit sandpaper and going up to 600 - grit, gradually increasing the fineness. Through this cycle of manual work, the surface is made smooth.
8. Coating: Choosing the most suitable one
Elitecustomtable chooses the most suitable coating in accordance with the specific material characteristics of each type of wood. Whether it is the SAICOS plant - based wood wax oil imported from Germany or the exclusively specially - developed water - based paint coating, all can ensure that the color and texture of the original wood remain vivid while also providing a tactile experience without any color loss.